Meningkatkan Efisiensi Industri melalui Design of Experiments dan Future State Map
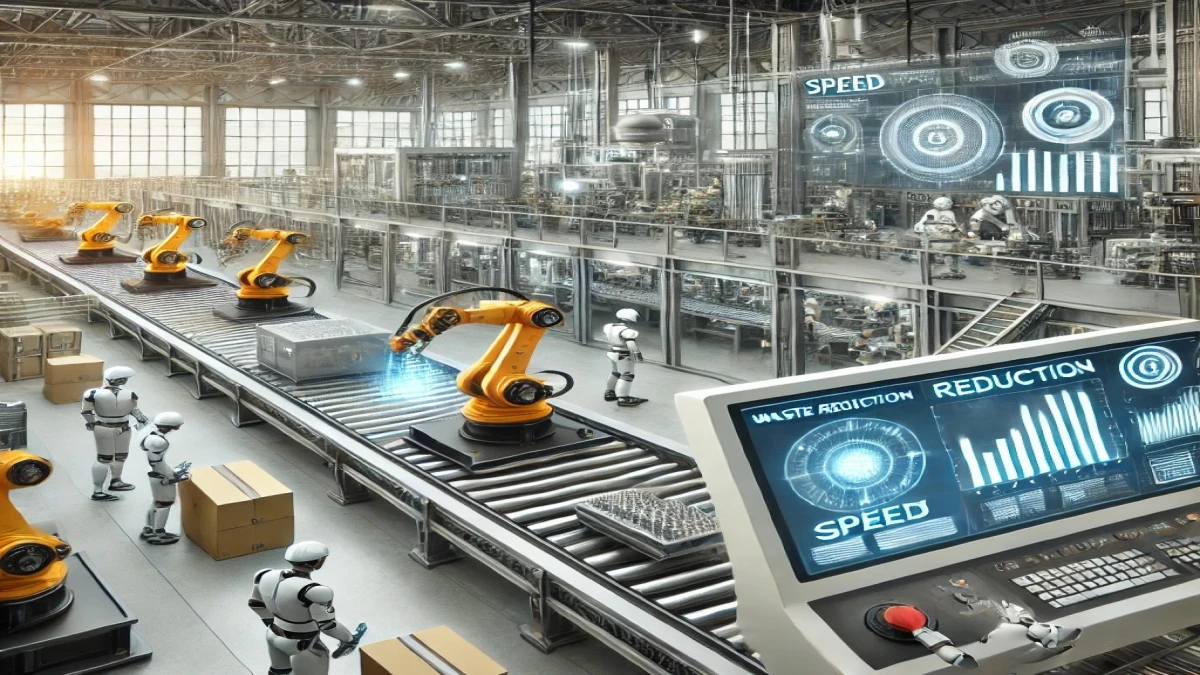
Meningkatkan Efisiensi Industri melalui Design of Experiments dan Future State Map.
Oleh:
Ari Nurdiansyah, Endriana Pratama, Muflih Fadhilah, Junior Researcher dan Supply Chain Indonesia
Metode statistik sistematis yang dikenal sebagai Desain of Eksperimen (DoE) pertama kali diperkenalkan oleh Sir Ronald A. Fisher dalam karyanya yang berjudul "The Design of Experiments" pada tahun 1930, dan melibatkan penerapan pendekatan analisis varians (ANOVA) sebagai metode utamanya untuk mengembangkan teori dan metode statistik. Desain of Eksperimen (DoE).
BACA JUGA: Bayang-Bayang Ketimpangan Jabar (Bagian II), Lahan Hilang, Rakyat Terpinggir
DoE mencakup perencanaan dan perancangan eksperimen. Ini termasuk menemukan faktor (variabel bebas) yang mempengaruhi respons (variabel terikat), menentukan tingkat faktor, dan mengatur tata letak eksperimen. Tujuannya adalah untuk mencapai kesimpulan yang masuk akal dan objektif secara efektif dan efisien.
Value Stream Mapping (VSM), yang merupakan bagian dari metodologi Lean Manufacturing, terdiri dari Future State Map (FSM). Ide tentang Value Stream Mapping pertama kali muncul pada tahun 1950-an oleh Toyota Production System (TPS), dan dilanjutkan oleh Taiichi Ohno dan Shigeo Shingo.
Namun, buku "Learning to See" (1999), yang ditulis oleh Mike Rother dan John Shook dari Lean Enterprise Institute, mempopulerkan istilah Future State Map (FSM) sebagai alat perbaikan VSM.
Oleh karena itu, meskipun tidak ada satu pun individu yang secara eksplisit disebut sebagai "penemu" Future State Map, ide ini dikembangkan dan dikembangkan dalam lingkungan manufaktur Lean, terutama oleh Toyota dan para peneliti Lean seperti Mike Rother dan John Shook.
Dalam Lean Manufacturing, Future State Map adalah alat yang dapat digunakan untuk menggambarkan kondisi ideal dari proses bisnis atau produksi di masa depan setelah perbaikan. Peta ini membantu perusahaan menemukan pemborosan dalam proses mereka saat ini dan membuat alur kerja yang lebih efisien dengan mengurangi atau menghilangkan aktivitas yang tidak bernilai. Analisis menyeluruh aliran material dan data diperlukan untuk membuat Peta Kondisi Masa Depan.
Design of Experiment (DoE)
Desain Eksperimen adalah suatu metode statistik yang diterapkan dalam penelitian eksperimen untuk meningkatkan kualitas produk dan proses (Costa, dkk. 2006). National Institute of Standards and Technology di Amerika Serikat mendefinisikan Desain Eksperimen sebagai pendekatan sistematis dalam menyelesaikan masalah teknik yang menggunakan prinsip dan teknik pada tahap pengumpulan data untuk mendukung kesimpulan yang valid (Firka, 2011).
Desain Eksperimen bertujuan untuk mengidentifikasi hubungan sebab-akibat antara output (variabel respon) dan faktor-faktor yang mempengaruhinya.
Dalam Desain Eksperimen, terdapat dua jenis variabel utama, yaitu variabel independen (faktor) dan variabel dependen (respon). Variabel independen dibagi menjadi dua kategori, yaitu faktor terkontrol (faktor yang dapat dikendalikan) dan faktor tidak terkontrol (kovarian), yang sering disebut sebagai faktor pengganggu (noise factor). Setiap faktor yang diuji memiliki sejumlah level. Perlakuan (treatment) merujuk pada kombinasi level dari semua faktor yang diuji dalam eksperimen, sedangkan replikasi menunjukkan jumlah pengulangan percobaan untuk perlakuan yang sama.
Ada beberapa alasan atau tujuan dalam melaksanakan eksperimen. Pertama, untuk mengidentifikasi penyebab variasi respon dari unit yang diamati dengan menentukan faktor-faktor yang berpengaruh. Kedua, untuk menemukan kondisi optimum dari respon yang diamati. Ketiga, untuk membandingkan respon dari berbagai perlakuan (kombinasi level) yang berbeda. Keempat, untuk membangun model respon.
Terakhir, untuk meminimalkan efek dari faktor tak terkontrol sehingga menghasilkan proses atau produk yang lebih robust. Secara keseluruhan, DoE memberikan pendekatan yang sistematis dan efisien dalam melakukan eksperimen, sehingga hasilnya lebih valid dan dapat digunakan untuk meningkatkan kualitas produk dan proses.